Enhancing Workplace Safety with Proper Pallet Box Handling
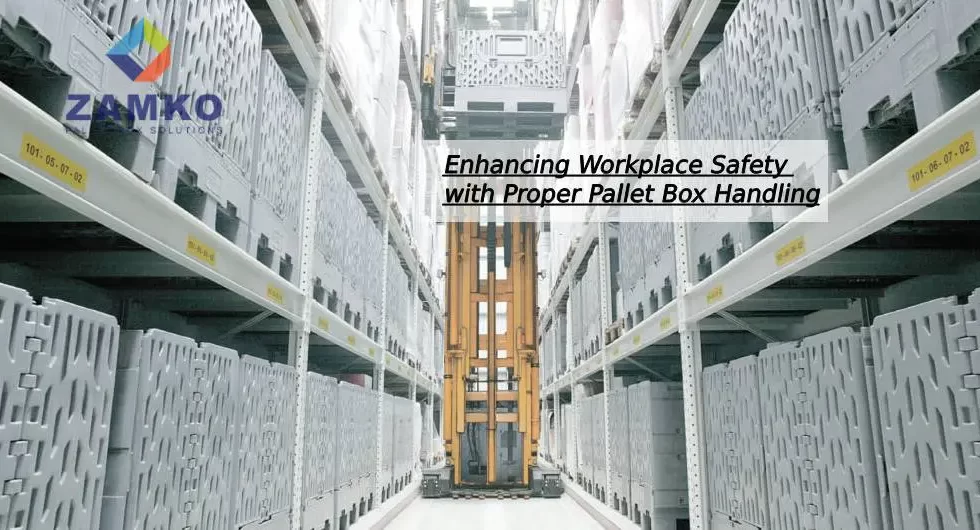
About workplace safety
The meaninig of Workplace Safety? The logistics and warehousing industry plays a critical role in driving global economies. Yet, it is also an industry rife with numerous health and safety challenges. One of the significant concerns revolves around the handling of pallet boxes – sturdy storage containers that play an essential part in the transport and storage of goods. In this article, we delve into the intricacies of pallet box handling and its potential implications for workplace safety.
Importance of Workplace Safety in Logistics
Workplace safety is a paramount concern across all industries. Still, it holds particular significance in logistics due to the nature of work, which often involves the handling of heavy goods, machinery operation, and a high potential for accidents. In 2019 alone, the US Bureau of Labor Statistics reported approximately 5.1 cases of nonfatal occupational injuries and illnesses per 100 full-time workers in the transportation and warehousing sector.
Promoting a safe work environment in logistics not only contributes to reducing the likelihood of accidents and injuries, but it also leads to enhanced productivity, employee satisfaction, and overall operational efficiency. A robust safety culture is an investment that pays dividends in the form of reduced workers’ compensation costs, lower turnover rates, and improved reputation among clients and partners.
Understanding Pallet Boxes
Pallet boxes are an integral component of the logistics and supply chain management. They are large containers used for the transportation and storage of various goods, from food items to heavy machinery parts. The design of these boxes allows for easy stacking, improving space efficiency in warehouses and during transportation. However, the variety in types and build of pallet boxes necessitates a comprehensive understanding for safe handling.
Types of Pallet Boxes
There are several types of pallet boxes, including wooden, plastic, metal, and cardboard, each serving different needs. Wooden pallet boxes are strong and durable, commonly used for shipping heavy items. Plastic pallet boxes are lightweight yet robust and are typically used for goods that require a higher degree of protection from the elements. Metal pallet boxes, often made from steel or aluminum, are used for extremely heavy or sensitive items due to their superior strength and durability. Cardboard or corrugated pallet boxes are used for lightweight items or one-time shipments due to their lower cost and recyclability.
Material and Build
The material and build of pallet boxes play a critical role in their handling safety. For instance, wooden pallet boxes can splinter or break, posing potential harm. On the other hand, plastic pallet boxes, although robust, can become brittle and crack under extreme temperatures. Metal boxes are durable but can be heavy to maneuver, posing a risk of injury. Cardboard boxes are light and easy to handle, but they can easily be damaged if mishandled or overloaded. Thus, understanding the properties and limitations of different pallet box materials is essential for safe handling and can significantly reduce the risk of workplace accidents.
Risks and Hazards in Pallet Box Handling
Handling pallet boxes in the logistics and warehousing environment poses several potential hazards. These risks can lead to physical injuries, damage to goods, and long-term health implications if not appropriately addressed. Understanding these risks is a crucial step towards implementing effective preventive measures.
Physical Injuries
Physical injuries are the most visible and immediate risk associated with pallet box handling. Workers can suffer cuts from sharp edges or splinters, especially when dealing with wooden or metal boxes. There’s also the risk of musculoskeletal injuries from improper lifting and carrying techniques. The heavy weight of some boxes can lead to back, shoulder, or knee injuries. Moreover, poorly stacked or unstable pallet boxes can topple over, causing crush injuries or even fatal accidents in severe cases.
Damage to Goods
Inappropriate handling of pallet boxes can also lead to damage to the goods being transported or stored. This could result in significant financial losses, not to mention the potential loss of trust from clients. For instance, overloading a pallet box or using the wrong type of box for specific goods could result in the box breaking, causing damage to the items inside. Mishandling could also result in boxes being dropped, causing shock damage to sensitive items.
Long-Term Health Implications
Apart from the immediate risks, improper pallet box handling can lead to long-term health problems. Continuous lifting and moving of heavy boxes can result in chronic musculoskeletal disorders, including repetitive strain injuries and chronic back pain. Workers exposed to damaged or deteriorating boxes, especially wooden ones, may also suffer from respiratory conditions due to dust or mold inhalation.
The Role of Proper Training in Pallet Box Handling
Given the potential risks involved, proper training in pallet box handling is crucial in promoting workplace safety. Such training can equip employees with the knowledge and skills necessary to safely carry out their tasks, thereby minimizing the risk of accidents and injuries.
Training Objectives
The primary objective of pallet box handling training is to educate workers about the various types of boxes, their unique characteristics, and the correct methods of handling them. This includes understanding the weight limits, appropriate lifting and stacking techniques, and the importance of regular inspections for damage. Training should also aim to foster a culture of safety, encouraging employees to look out for potential hazards and report any concerns promptly.
Types of Training Methods
Different training methods can be employed to achieve these objectives. Classroom-style instruction can provide workers with the foundational knowledge about pallet boxes and handling techniques. Hands-on training, on the other hand, allows employees to put this knowledge into practice in a controlled environment, enabling them to develop the necessary skills and confidence before handling real tasks.
In addition to these, utilizing digital platforms for online training modules can offer flexibility, allowing employees to learn at their own pace. Simulation-based training, using virtual or augmented reality, can also be an effective method, providing a realistic yet safe environment for workers to practice handling pallet boxes.
Equipment for Safe Pallet Box Handling
Ensuring workplace safety in pallet box handling isn’t just about training; it also involves equipping your employees with the right tools and protective gear. Using proper equipment can greatly reduce the risks associated with manual lifting and transportation of heavy pallet boxes, and protective gear can safeguard employees from potential injuries.
Pallet Trucks
Pallet trucks, also known as pallet jacks or pump trucks, are one of the most commonly used pieces of equipment for pallet box handling. These machines are designed to lift and move pallet boxes easily and efficiently. They come in manual and electric versions.
Manual pallet trucks are operated by manually pumping a lever to lift the pallet box off the ground, then pushing or pulling the truck to move the box. These are most suitable for lighter loads and shorter distances. Electric pallet trucks, on the other hand, are powered by a motor and are more suitable for heavier loads and longer distances. They require less physical exertion from the operator, reducing the risk of strain injuries.
In addition to standard pallet trucks, there are specialized variants designed for specific situations. High-lift pallet trucks can elevate boxes to higher levels for stacking or to work at a comfortable height, and all-terrain pallet trucks can handle uneven surfaces, ideal for outdoor operations.
Forklifts
For larger and heavier pallet boxes, forklifts are an essential tool. These vehicles are capable of lifting and moving heavy loads over considerable distances. They also allow for the stacking of boxes at great heights, making efficient use of warehouse space. However, forklift operation requires specialized training to ensure safe and efficient use. Regular maintenance checks are also essential to keep these machines in good working condition and prevent accidents due to mechanical failures.
Gloves and Protective Gear
Beyond the machinery, personal protective equipment (PPE) plays a crucial role in enhancing workplace safety during pallet box handling. For instance, gloves can protect workers’ hands from cuts and scrapes when handling boxes, particularly those made of wood or metal. Gloves with good grip can also help prevent accidental slips while lifting and carrying boxes.
Safety footwear with steel toe caps can protect feet from heavy falling objects, while high-visibility clothing can ensure that workers are easily seen in busy work environments, reducing the risk of collisions. Helmets can protect against head injuries in case of falling objects, and back supports can help prevent strain injuries when lifting heavy boxes.
Equipping your workforce with the right tools and protective gear not only reduces the risk of accidents and injuries, but it also demonstrates your commitment to workplace safety. This can boost employee morale and productivity, leading to better overall performance.
Implementing Safe Handling Procedures
Establishing safe handling procedures is a fundamental step in promoting workplace safety in pallet box handling. These procedures should cover all aspects of the handling process, including correct lifting techniques, appropriate load stacking, and regular equipment maintenance.
Correct Lifting Techniques
One of the most common causes of workplace injuries in logistics is incorrect lifting techniques. When lifting heavy items such as pallet boxes, there’s a significant risk of back injury if the correct lifting method is not employed.
A proper lifting technique involves keeping a wide stance with one foot slightly ahead of the other for balance. The lifter should then squat down, keeping the back straight, bending the knees and keeping the box close to the body. The lift should be performed using the leg muscles, not the back. Upon lifting, avoid twisting the body, instead turn by moving the feet.
Training sessions can be instrumental in educating employees on correct lifting techniques, emphasizing the importance of using leg muscles rather than the back and keeping the load close to the body to maintain balance.
Appropriate Load Stacking
Proper load stacking is critical in preventing accidents like toppled loads or unstable stacks. There are several key principles to consider for safe load stacking:
-
Heaviest items should always be placed at the bottom of the stack to ensure stability.
-
The stack should be arranged to prevent items from sliding or falling.
-
There should be clear access to all pallet boxes to avoid reaching over or moving other boxes unnecessarily, which can cause instability.
-
The height of the stack should not exceed the recommended limit to prevent toppling.
Additionally, the use of pallet wrappers or strapping can help secure stacked boxes, further reducing the risk of accidents.
Regular Equipment Maintenance
Regular equipment maintenance is essential in preventing accidents and ensuring the smooth running of operations. This includes routine checks and servicing of handling equipment like forklifts and pallet trucks.
An equipment maintenance checklist can include:
-
Checking the condition of wheels and tires for any wear or damage.
-
Ensuring the brakes are functioning correctly.
-
Ensuring all safety features, like warning sounds or lights, are operational.
-
Checking the condition of the lifting mechanism for any faults or signs of strain.
-
Checking battery levels and charging regularly for electric pallet trucks and forklifts.
By strictly adhering to maintenance schedules and promptly addressing any identified issues, you can ensure the longevity of your equipment and the safety of your workforce. A well-maintained piece of equipment is less likely to malfunction, reducing the risk of accidents that could lead to injuries or damage to goods.
The Concept of Reusable and Returnable Packaging in Workplace Safety
The logistics and supply chain industry has seen significant transformations in recent years. One such innovation that is gaining widespread acceptance is the concept of reusable and returnable packaging. It’s not just an eco-friendly choice; it also has noteworthy implications for workplace safety.
Overview of Reusable and Returnable Packaging
Reusable and returnable packaging is the practice of using durable containers, pallets, hand-held containers, dunnage, and other transport packaging systems that can be reused multiple times. These items, made from sturdy materials such as plastic, metal, or wood, are designed for extended life, often in a closed-loop system. Instead of the traditional single-use packaging, these containers are returned to the supplier or manufacturer after delivery for cleaning, repairing if necessary, and reuse.
Examples of returnable and reusable packaging include plastic pallet boxes, foldable pallet boxes, metal containers, plastic crates, and pallets. They have robust construction and are built to withstand the harsh conditions of logistics and transportation. They are also designed for ease of handling and storage, often being stackable or collapsible when not in use.
Benefits for Workplace Safety
Reusable and returnable packaging brings several workplace safety benefits to the table. By adopting these systems, businesses can reduce the risks and hazards associated with pallet box handling.
Reduced Handling and Physical Strain: One of the most significant advantages of reusable and returnable packaging is the reduction in physical handling. Because these containers are designed to be used multiple times, there is less need for constant unpacking and repacking of goods. This leads to a decrease in manual handling, which reduces the physical strain on workers and consequently minimizes the risk of injuries. For instance, collapsible or foldable pallet boxes, when not in use, can be quickly folded down, thus reducing the storage space needed and the effort to move them around.
Greater Durability and Stability: Reusable and returnable packaging systems are designed to be robust and sturdy, which means they provide better protection for goods and, at the same time, are less likely to collapse or fall apart under stress. This added stability minimizes the risk of accidents caused by the packaging failing under the load, preventing damage to goods and potential injuries to workers.
Design Features Enhancing Safety: Many reusable and returnable packaging options are designed with features that enhance safety. For example, they may include ergonomically designed handles, making it easier and safer for workers to lift and carry them. Some containers might also feature locking systems that secure the load during transport, reducing the risk of goods falling out and causing an accident.
Consistency and Familiarity: Using the same types of reusable packaging over and over can breed familiarity and thus reduce accidents caused by unfamiliar or inconsistent packaging. Workers can become proficient in handling these packages, knowing their weight and how they balance, leading to safer operations.
By understanding the impact of reusable and returnable packaging on workplace safety, businesses can leverage these systems to reduce injuries, increase efficiency, and build a safety-first culture in their logistics operations.
Innovative Solutions for Safe Pallet Box Handling
As the world of logistics and supply chain management evolves, innovative solutions that streamline processes while enhancing workplace safety are emerging. This is particularly true for pallet box handling, where new designs and materials are helping to mitigate the risks and challenges involved. Let’s delve into two key innovative solutions: foldable pallet boxes and custom pallet boxes.
Foldable Pallet Boxes
Foldable pallet boxes have emerged as a revolutionary solution in the logistics sector. By combining durability, flexibility, and space efficiency, these containers significantly contribute to the safety and efficiency of operations.
Pros:
-
Space Efficiency: Foldable pallet boxes, as the name suggests, can be folded when they’re not in use. This significantly reduces their volume, freeing up valuable storage and transportation space. More importantly, it makes handling these containers safer and more efficient, as fewer resources are needed to transport, store, or rearrange them.
-
Durability: Foldable pallet boxes are typically made from robust materials like plastic or metal, making them resistant to wear and tear. This durability translates to safer operations, as the risk of accidents due to broken or damaged boxes is substantially reduced.
-
Versatility: These boxes are suitable for a wide range of goods, which simplifies operations and enhances safety. The familiarity of handling a consistent type of container reduces errors and accidents.
Cons:
-
Higher Initial Cost: While foldable pallet boxes offer numerous benefits, they may come with a higher initial cost than traditional pallet boxes. However, their longevity and efficiency often result in long-term savings.
-
Maintenance: These boxes require regular maintenance checks to ensure their folding mechanisms remain in good working order.
Custom Pallet Boxes
Custom pallet boxes are another innovative solution that is reshaping the logistics landscape. These boxes are designed to meet specific requirements, ensuring an optimal fit for the goods they’re intended to carry.
Pros:
-
Enhanced Protection: By creating a perfect fit for the goods, custom pallet boxes provide superior protection during transit, reducing the risk of damage to the products and potential injuries to workers due to shifting loads.
-
Improved Efficiency: Custom boxes can enhance operational efficiency by eliminating wasted space and reducing the need for additional packaging materials. This not only cuts down costs but also reduces handling efforts, contributing to workplace safety.
-
Brand Promotion: Custom pallet boxes can be designed with a company’s branding, serving as a powerful marketing tool. This aspect, while not directly related to safety, contributes to overall business benefits.
Cons:
-
Higher Costs: Custom designs often come at a premium. The additional costs for design and manufacturing need to be justified by the benefits in terms of safety, efficiency, and marketing.
-
Lead Times: The process of designing and manufacturing custom pallet boxes can take longer than purchasing standard boxes, which may not be ideal for businesses with tight deadlines.
In summary, foldable and custom pallet boxes present innovative ways to enhance workplace safety in the logistics sector. The key to successful implementation lies in thoroughly analyzing your needs, assessing the pros and cons, and choosing the solution that provides the most benefits for your specific operations. It is important to remember that investing in safety is an investment in the sustainability and success of your business.
Case Study: Success Stories in Implementing Safe Pallet Box Handling
In the rapidly evolving logistics sector, many businesses are turning to innovative solutions to enhance workplace safety and efficiency in pallet box handling. To highlight the tangible benefits of these solutions, let’s explore the success stories of two companies that have significantly improved their operations through the implementation of safe pallet box handling practices.
Automotive 1st tier supplier Embracing Foldable Pallet Boxes
This customer is a leading manufacturer of automotive components, shipping their products to various assembly plants across the globe. Despite their success, the company was facing challenges in terms of shipping costs, warehouse utilization, and workplace accidents related to pallet box handling.
In response to these challenges, our client chose to invest in foldable pallet boxes. The initial cost was substantial, yet the company recognized the potential long-term savings and safety enhancements this innovative solution could provide.
Over the course of a year, our customer observed significant improvements. The foldable pallet boxes minimized the volume of empty containers during return shipping, reducing transportation costs by 35%. Warehouse space was maximized, resulting in a 50% increase in storage efficiency. More importantly, due to the robust design and ease of handling of foldable pallet boxes, workplace accidents linked to pallet box handling reduced by 70%. The company’s decision to embrace this innovative solution significantly enhanced their operations and amplified their commitment to workplace safety.
Electronics manufacturer Investing in Custom Pallet Boxes
This high-tech electronics manufacturer, was struggling with product damage during shipping and increased costs associated with excess packaging materials. The traditional pallet boxes they were using did not provide the perfect fit for their products, resulting in shifting loads and potential damage.
Recognizing the need for a more tailored solution, our customer decided to invest in custom pallet boxes, designed specifically for their products. Although the upfront cost was higher than standard pallet boxes, the company believed in the long-term benefits this solution could provide.
The results exceeded their expectations. The custom pallet boxes provided an optimal fit for their products, substantially reducing damage during shipping. In fact, over a period of one year, product damage decreased by 80%. In addition, the perfect fit of the custom boxes eliminated the need for extra packaging materials, leading to a 40% reduction in packaging costs. Notably, the stable and predictable nature of handling these custom boxes contributed to a safer workplace environment, with a 60% decrease in accidents associated with pallet box handling.
Both companies made strategic decisions to invest in innovative pallet box solutions, resulting in significant improvements in their operations. Their experiences underline the value of adopting safe pallet box handling practices. Such decisions not only lead to cost savings and enhanced efficiency but also contribute to creating a safer and more productive working environment.
These case studies are a testament to the adage that investing in safety is an investment in the sustainability and success of your business. Therefore, when considering the safety measures for your logistics operations, remember to consider the options of foldable and custom pallet boxes. Their benefits, as illustrated by the successes of the above mentioned 1st tier Automotive supplier and the Electronics manufacturer, may well be the key to enhancing your operational efficiency and workplace safety.
Enhancing Workplace Safety with Proper Pallet Box Handling
Workplace safety is a paramount concern in the logistics industry. The effective handling of pallet boxes can substantially reduce workplace accidents, increase productivity, and improve overall operational efficiency.
The right pallet box can make all the difference. Whether it’s the robust and reusable plastic pallet boxes, the cost-effective carton pallet boxes, the traditional wooden pallet boxes, or the heavy-duty steel pallet boxes, choosing the right box for your needs can enhance safety and efficiency in your operations.
Innovative solutions like foldable and custom pallet boxes can lead to significant improvements. These boxes not only reduce transportation and storage costs but also minimize the risk of workplace accidents. As demonstrated by the success stories of 1st tier Automotive supplier and the Electronics manufacturer, investing in these solutions can yield considerable long-term benefits.
It’s essential to remember that ensuring workplace safety is not a one-off effort. It’s an ongoing process that requires proper training, regular equipment maintenance, and the continuous improvement of handling procedures.
So, if you’re in the logistics industry, it’s time to take a fresh look at your pallet box handling practices. Embrace the right equipment, adopt the appropriate handling techniques, and choose the most suitable pallet boxes for your operations. And remember, in this quest for safety, you’re not alone. Companies like Zamko are ready to guide you in choosing the right pallet boxes and implementing effective and safe handling procedures.
At Zamko, we offer a wide range of pallet boxes to meet the diverse needs of our customers. Whether you need plastic pallet boxes, carton pallet boxes, wooden pallet boxes, or steel pallet boxes, we have you covered. Check out our products and start your journey towards a safer and more efficient workplace today!